PIR Sandwich Panels – High-Performance Insulation & Fire Protection by Square Panel System Co., Ltd.
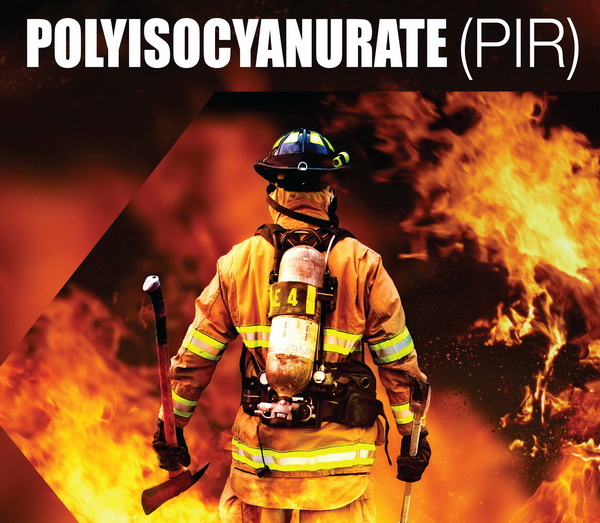
Why Choose Square Panel System Co., Ltd. for PIR Insulation Panels?
- High-Quality PIR Panels – Advanced fire resistance and excellent thermal insulation properties
- Proven Fire Safety Performance – Successfully tested under ASTM E84 and UBC 26-3 standards
- Durability & Energy Efficiency – Long-lasting insulation solution that reduces heating and cooling costs
- Compliance with International Standards – Approved by FM Global, ASTM, BS, JIS, and DIN
- Eco-Friendly & Sustainable – Manufactured with CFC-free, environmentally responsible technology
Get the Best PIR Insulated Panels for Your Project
If you are looking for PIR Panels, PIR Sandwich Panels, or PIR Insulation for warehouses, cleanrooms, food storage facilities, pharmaceutical plants, or high-rise buildings, Square Panel System Co., Ltd. offers customized solutions to meet your project’s needs.
Contact us today to learn more about our PIR Insulated Panels and get a quote for your next construction project.
Square Panel System Co., Ltd. is a leading
manufacturer of PIR Panels and PIR Sandwich Panels, offering cutting-edge insulation solutions for over 25 years. Our high-quality PIR Insulation panels are widely used across multiple industries, including food processing, pharmaceuticals, electronics, and high-rise construction such as knock-down houses, condominiums, and commercial buildings. With advanced production technology, we provide durable, energy-efficient, and fire-resistant PIR Insulated Panels that meet global safety and performance standards.
Innovative PIR Insulation Panels – Superior Fire Resistance & Thermal Efficiency
At Square Panel System Co., Ltd., we have developed an advanced Polyisocyanurate (PIR) foam panel using a Discontinuous Production System. Our PIR Sandwich Panels offer exceptional fire resistance, superior insulation properties, and outstanding thermal conductivity (K = 0.024 W/m.K), making them an excellent alternative to polyurethane (PU) foam. These characteristics ensure better energy efficiency, reduced cooling costs, and long-term durability for various applications.
Fire-Resistant PIR Panels Tested & Certified for Safety
Our PIR Insulation panels have been rigorously tested by the Faculty of Engineering, Chulalongkorn University, achieving compliance with international fire safety standards such as:
- ASTM E84 – Standard Test Method for Fire Resistance
- Uniform Building Code (UBC) 26-3 – Room Fire Test for Interior Foam Plastic Systems
Thanks to their superior fireproofing properties, PIR Panels from Square Panel System Co., Ltd. are recognized and accepted by global institutions including FM Global, ASTM, BS, JIS, and DIN STANDARD. These certifications demonstrate the high safety and reliability of our PIR Insulated Panels for use in industrial, commercial, and residential projects.
Eco-Friendly PIR Sandwich Panels – Sustainable & CFC-Free Manufacturing
At Square Panel System Co., Ltd., we utilize a state-of-the-art, environmentally friendly production process, free from chlorofluorocarbons (CFCs). Our PIR Sandwich Panels not only enhance thermal insulation and fire protection, but they also contribute to sustainable building solutions by reducing energy consumption and carbon footprint.
Executive Summary
A Study of Ignition Behaviour of Wall and Ceiling System Project
Centre of Engineering Research and Technical Services Faculty of Engineering Chulalongkorn University
September 2013
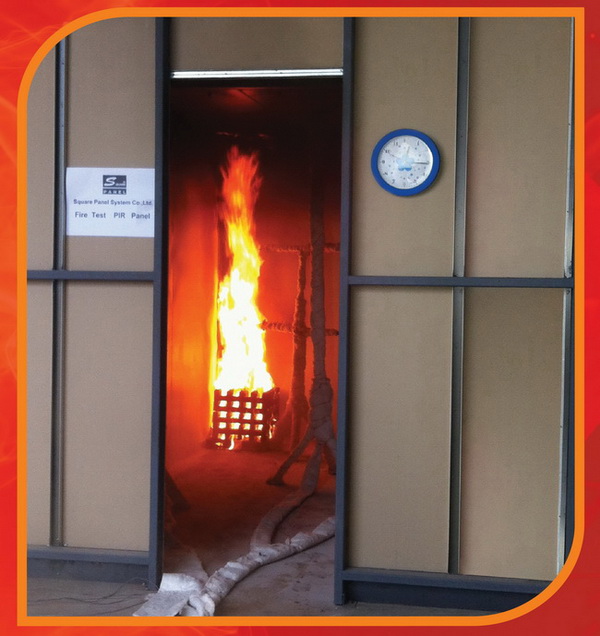
Test results in accordance with UBC26-3 standard
The observation during the test
The observation began when the crib started igniting. Video tape and photograph were used to record the observation before and during the test for considering ignition behaviour of product. Details of the observation were shown in table1 and the duration of observation was 15 minutes.
The observation began when the crib started igniting. Video tape and photograph were used to record the observation before and during the test for considering ignition behaviour of product. Details of the observation were shown in table1 and the duration of observation was 15 minutes.
Table1 Information of the observation during the test
Time (min:sec) | Details of test observation |
0:00 | Flames start igniting wood excelsior. Light smoke from burning wood excelsior spreads around test room but still can observe inside walls. |
1:00 | Flames ignite all over wood excelsior. |
1:30 | Noises are made intermittently from the expansion of steel wrapping of product. |
2:00 | Flames reach 150 cm. above wood excelsior. (Thermocouple#2) |
4:15 | Flames reach to ceiling. Product colour starts breaking. Product expands. |
5:00 | The edge of walls and ceiling around the crib start being charred. |
6:00 | White smoke spreads out of joints of floor and wall and wall and ceiling. |
8:00 | Corners of the crib start igniting. |
10:30 | White smoke spreads out of the side and doorway. Flames ignite the crib severely. |
12:00 | Black smoke is generated above the crib and spread in test room. Flames ignite the crib more severely. |
15:00 | End test. The fire was extinguished by using chemicals and water. |
Measured Temperature
During the test, Thermocouples were installed at 5 positions (#1-#5) as shown in figure 1 and 2, and measured temperatures during the test were shown in figure 3. Within 4 minutes from the beginning of the test, temperature above the crib reached the highest point at 580°C - 720°C. Measured temperatures from the other thermocouples in test room got higher according to period of time. After the test started, average temperature in test room was below 600°C throughout 15 minutes of the test.
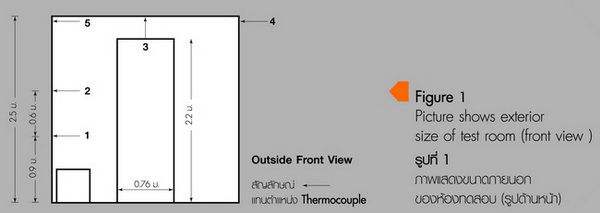
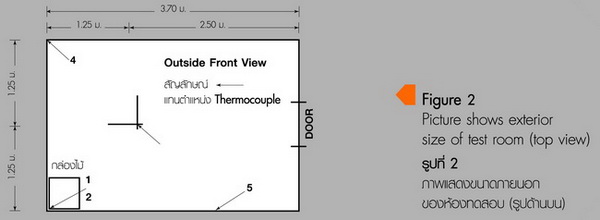
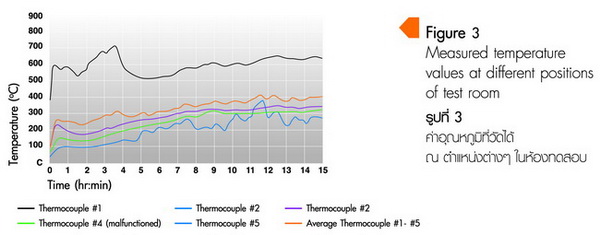
Conclusions
When consider the information from the observation throughout 15 minutes of the test in accordance with the UBC26-3 standard as described above found that
NOTE :
According to UBC8-2, if flames ignite out of test room and top surface temperature in the middle of test room reaches approximately 600°C. Ignition behaviour may consider to be severe and dangerous.
- No flames spread out of the front doorway of test room or flashover
- Product didn't not produce excessive smoke.
- Charring did not extend to the outside edge of sandwich panel sides that did not contact to the fire.
NOTE :
According to UBC8-2, if flames ignite out of test room and top surface temperature in the middle of test room reaches approximately 600°C. Ignition behaviour may consider to be severe and dangerous.
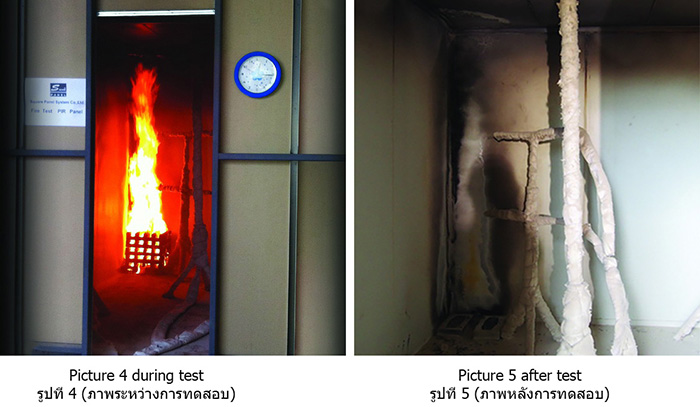
Results of test model in accordance with ASTM E84 standard
In this content contains test results of flame spread behaviour and calculating flame spread index of Polyisocyanurate (PIR) sandwich panel of Square Panel System Co., Ltd. Test apparatus and environmental control during the test were modelled in accordance with ASTM E84 standard. Test operated on 2 specimens which each of them were 10 cm. thick. They were provided and installed by Square Panel System Co., Ltd. Test results would be used for evaluating flame spread behaviour and basic product safety under fire conditions.
Test apparatus model
This test model specified length of test apparatus as 3.5 m, but cross section area still had size following the standard as shown in figure 6 - 7.Test apparatus model consisted of gas burner which connected to liquid fuel and ventilation fan at opposite end. Smoke density detector was not installed in this model, so smoke- developed index value could not be calculated.
Test apparatus model
This test model specified length of test apparatus as 3.5 m, but cross section area still had size following the standard as shown in figure 6 - 7.Test apparatus model consisted of gas burner which connected to liquid fuel and ventilation fan at opposite end. Smoke density detector was not installed in this model, so smoke- developed index value could not be calculated.
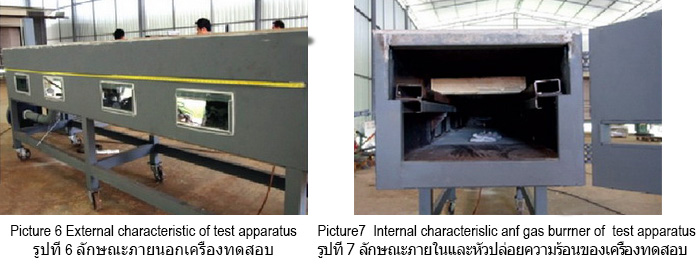
Test procedure
The test started by installing and laying test specimens which were 60 cm. wide x 300 cm. length horizontally on the edge of supporters in the tunnel. Flame released for heating under specimens for 10 minutes. Flame spread distance was observed every 30 seconds at observation windows. Graph of flame spread distance versus time was plotted and curve characteristic was adjusted to meet standard requirement (Curve characteristic only increases or remains stable). Area under the curve was used to calculate flame spread index.
Test limitation
This test can not use for testing with material that will peel off or melt under heat conditions
The test started by installing and laying test specimens which were 60 cm. wide x 300 cm. length horizontally on the edge of supporters in the tunnel. Flame released for heating under specimens for 10 minutes. Flame spread distance was observed every 30 seconds at observation windows. Graph of flame spread distance versus time was plotted and curve characteristic was adjusted to meet standard requirement (Curve characteristic only increases or remains stable). Area under the curve was used to calculate flame spread index.
Test limitation
This test can not use for testing with material that will peel off or melt under heat conditions
Environmental control during the test
- Ventilation which affect to flame characteristic was controlled
- Temperature in the test was around 500°C. Before starting the test, the height of gas burner and released gas temperature were calibrated to meet standard requirement. Temperature was controlled by inserting incombustible fiber cement board at the edge of supporters in the tunnel and measured temperature on the surface of material above the flame.
Flame spread distance was measured by observing characteristic and distance of flame which were generated from test material (flame which was generated by gas burner was not considered) as shown in figure 8 - 9. The test results of flame spread were shown in graph 3. Flame spread distance versus time graph and value adjustment in according to standard was shown in figure 10 - 11. Calculated flame spread index* (FSI) values were given below.
- Flame spread index of Specimen 1 = 5 (Measured FSI value = 4.3)*
- Flame spread index of Specimen 2 = 5 (Measured FSI value = 4.4)*
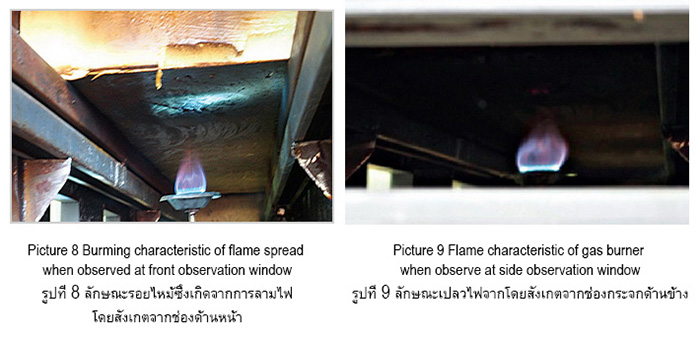
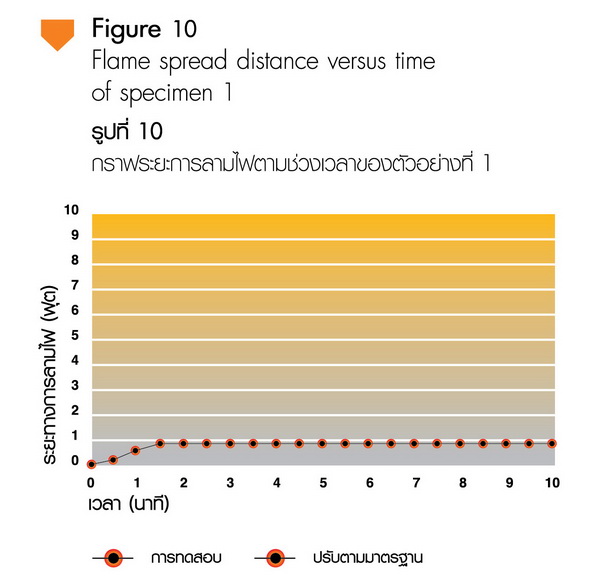
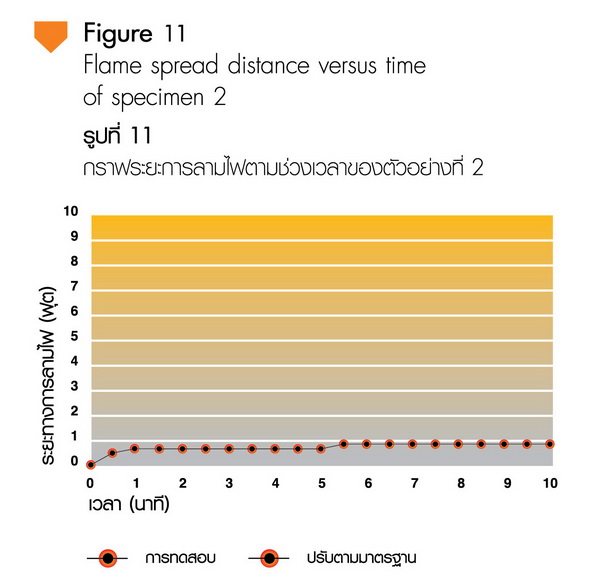
Combustion Characteristic
Specimen 1 : The highest distance of flame spread was 11 inches. Flames could be observed from the crack of material at minute 8:15. After the test, there was a 1 foot wide crack on the material as shown in figure 12.
Specimen 2 : The highest distance of flame spread was 11 inches. Flames could be observed from the crack of material at minute 8:00. After the test, there was a 1 foot wide crack on the material as shown in figure 13. The appearance was similar to sample 1.
Specimen 2 : The highest distance of flame spread was 11 inches. Flames could be observed from the crack of material at minute 8:00. After the test, there was a 1 foot wide crack on the material as shown in figure 13. The appearance was similar to sample 1.
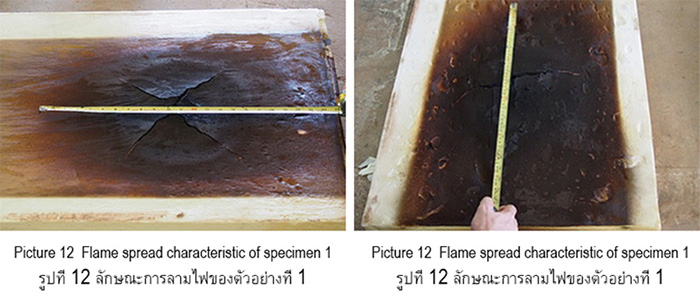
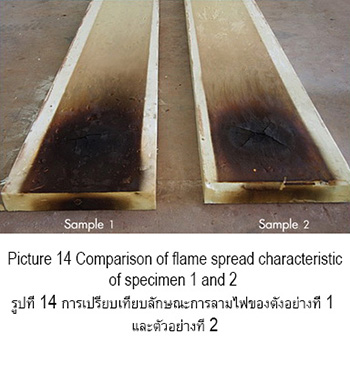
Conclusions
Considering data of flame spread index of specimens, this material tend to be classified as class A according to ASTM standard E84 (Flame Spread index 0.25 foot-minute; smoke-developed index 0 - 450) However smoke density could not be measured for calculating smoke-developed index in this test. So to classify certain class, further testing will be required as per standard.